Rubber was pretty simple before compounds came along
Prior to compounding, natural rubber used commercially had its limitations. Fortunately, through a series of accidents and inventions, rubber has evolved to become the wonder material that’s used almost everywhere today.
The world is working with and producing more custom rubber compounds than ever before, and companies like AirBoss continue to expand the spectrum. But what exactly is a rubber compound, and what makes them so important, common, and reliable when it comes to everyday products?
Let’s peel back the top layer and peek a little deeper into rubber compounds.
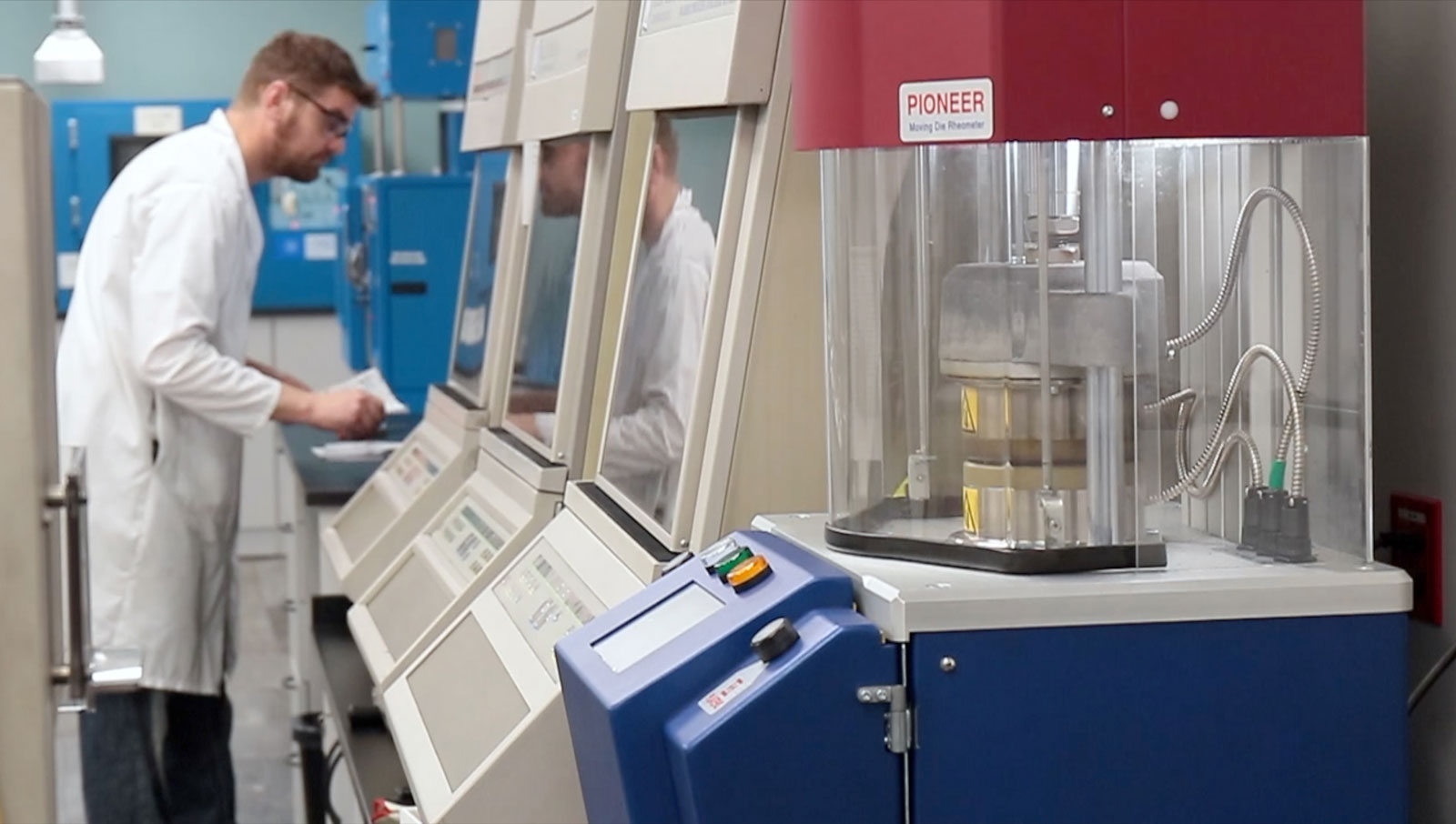
What is a Rubber Compound?
Basically, every advancement in rubber manufacturing since Charles Goodyear patented the vulcanization process has been a unique improvement.
Rubber in its purest form is harvested directly from rubber trees, and it’s when we start adding things to natural, pure rubber that we get rubber compounds. Goodyear’s vulcanization process added sulfur to rubber and then heated it up until it hardened.
Other early advancements in rubber compounding included the creation of neoprene rubber (polymerizing the hydrocarbon chloroprene), silicone rubber (curing, vulcanizing, and catalyzing silicon), EPDM rubber (vulcanizing ethylene, propylene, and diene monomers), and many more mixtures that are common compounds today.
Have a unique rubber challenge? Need professional insight?
The Most Common Rubber Compounds and Why They’re Special
Rubber, when you stop and think about it, is used in just about everything from the shoes on our feet to the tires on our streets and all the in-betweens. No single rubber—natural or synthetic—is responsible for all of the products we use on a daily basis, and new compounds continue to be created.
Here’s a list of the most common rubber compounds and what makes them special:
- Natural Rubber/Styrene-Butadiene Rubber/Butadiene blend (NR/SBR/BR) is a common polymer blend of general synthetic rubbers for multi-use purposes. It shares similar properties with general-purpose natural rubber and is often used in off-the-road (OTR) tires.
- Styrene-Butadiene Rubber/Butadiene blend (SBR/BR) is a wide-use application polymer rubber blend often used in things like shoe soles, seals, and various rubber belts. Butadiene (BR) is a polymer that is generally used together with other polymers to improve compound abrasion properties.
- Ethylene Propylene Diene Monomer Rubber (EPDM) is a more complex rubber compound that improves on the heat tolerance, elasticity and ozone/UV resistance of natural rubber. It is used widely in automotive seals and as an electrical insulator among other things.
- High heat EPDM is an AirBoss-proprietary compound called HeatBoss rubber that’s optimized for use in extreme high-heat applications like automotive damping and foaming products.
- Chloroprene Rubber (CR) has a good balance of properties that include temperature tolerances, flame resistance, and general chemical stability. This makes it ideal for things like gaskets, wire insulation, and rubber belts.
- Chlorinated Polyethylene Rubber (CPE) is similar to but not the same as CR. CPE rubber shares advanced sealant, temperature tolerance, and damping properties. It’s often used in water seals, and things like automotive hoses.
- Epichlorohydrin Rubber (ECO) is a unique polymer blend with high heat and oil resistance. It’s widely used in automotive parts of all types.
- Nitrile Rubber, Hydrogenated Nitrile Rubber blends (NBR, HNBR) is a butadiene-derived rubber compound exceptionally good at chemical and oil resistance. It’s often used in things like oil hoses and seals as well as disposable lab and examination gloves.
- Nitrile/Plastic blend (NBR/PVC, NBR/SBR/NR) is an easier-processed nitrile rubber blend that’s more cost-effective but slightly less resistant in some ways. It’s used in things like fire hoses, stators, and rollers.
- Butyl Rubber, Butyl Rubber/Natural Rubber blend (IIR, IIR/NR) is an isobutylene and isoprene polymer that has good resiliency/durability properties. As a result, it’s often used in things like defense boots and gloves, tire liners, and sealants.
- Silicone Rubber is a family of elastomer polymers that’s ideal for high-heat applications and often used in many different automotive heat-resistant parts.
- Fluorine Rubber (FKM) is a high-end fluorocarbon-based fluoroelastomer used in industries like aerospace engineering. It’s more expensive than others listed above and more optimized for oil and heat resistance for use in things like high-end gaskets.
Believe it or not, this is only scratching the surface of modern custom rubber compounds, but these are the most common. AirBoss engineers who work alongside customers needing exceptional performance continue to create unique compounds that push the limits of what synthetic rubber can do.
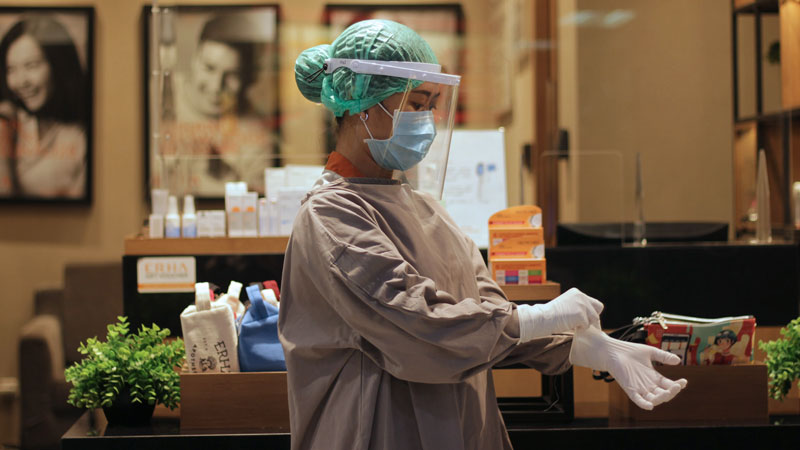
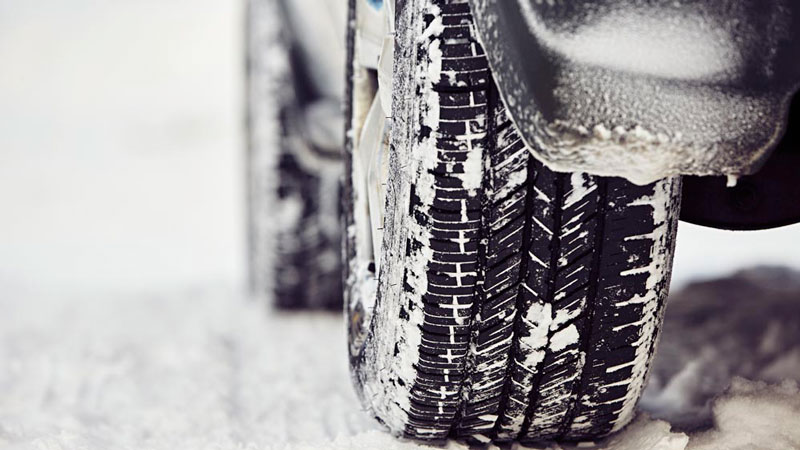
Why Custom Rubber Compounds Create Unique Application Opportunities
As mentioned above, custom rubber compounds extend and expand the functionality of natural rubber. This means AirBoss can design a custom compound that’s more reliable, performs better, and lives longer than a natural rubber counterpart.
Broadly, custom rubber compounds—from the simplest to the most complex—can be created to:
- Improve durability
- Increase temperature tolerances
- Maximize chemical resistances
- Meet exact density specifications
- Improve seal performance
- Increase flexibility
- Optimize processability
The Future of Rubber Compounds at AirBoss
AirBoss continues to evolve different rubber compounds to meet industry demands.
Proprietary compound families like HeatBoss, DuraBoss, and EcoBoss are mixed in ways that are designed to maximize properties like heat resistance, durability, and sustainability. As a result, customers keep coming to AirBoss with unique application challenges that we’re able to solve with any number of common and not-so-common custom rubber compounds.