Rubber is rubber, right? Wrong. There are more types and combinations of rubber and rubber compounds than you might imagine. Many rubber products are in plain sight—like rubber tires on your vehicle or rubber soles on your shoes—and many others are more subtle and nuanced.
The type of rubber and the complexity of a custom rubber compound varies based on a wide variety of application requirements. High-quality rubber manufacturers like AirBoss specialize in perfecting compounds to meet specific customer demands, and we’ve gotten pretty good at it.
However, we understand that not everyone is a rubber expert. Here’s what you should know about different types of rubber and what makes rubber compounds so special.
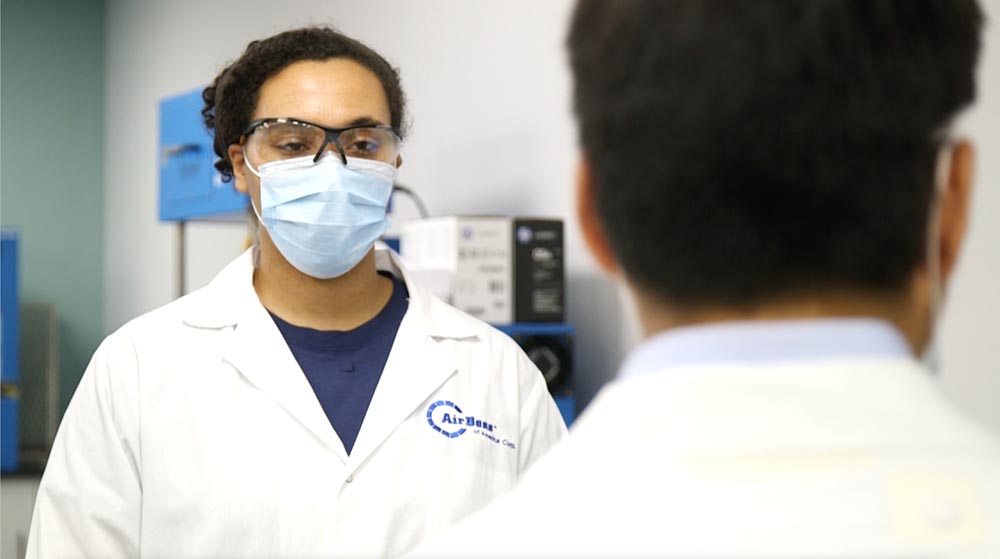
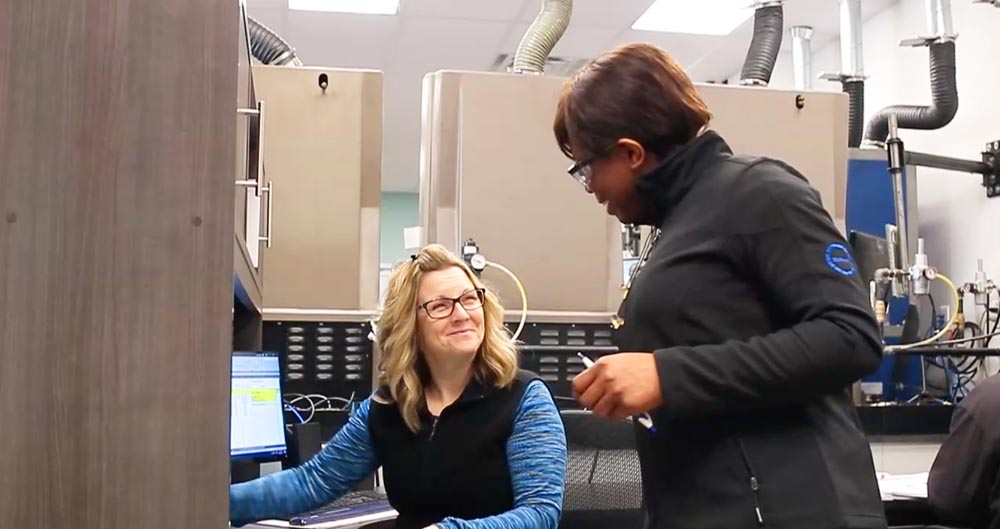
Natural and Synthetic Rubber
Natural rubber was first discovered in the Amazon River Valley in South America some time in the late 1400s. Over the following 500 years, rubber was refined, vulcanized, and compounded in ways that changed the world.
All modern rubber fits into two categories: natural rubber and synthetic rubber. While natural rubber has gone relatively unchanged since its discovery, synthetic rubber has been specialized in remarkable ways.
Natural Rubber
Natural rubber today is mostly polyisoprene, which is a naturally occurring polymer found in hevea (rubber) trees and guayule plants. The general composition has stayed the same over time, and organizations like the Global Platform for Sustainable Rubber work to keep it that way.
Natural rubber works well in applications that involve alcohols, some acids, and oxygenated solvents.
Synthetic Rubber
Synthetic rubbers are either general-purpose rubbers or specialty rubbers and are created by combining different polymers, monomers, and laminates. Early synthetic rubbers were petroleum-based and invented when natural rubber was more expensive and harder to come by.
Common synthetic rubbers include:
-
-
- Styrene-Butadiene Copolymer (SBR)
- Polybutadiene (BR)
- Isobutylene-Isoprene Copolymer (IIR, CIIR, BIIR)
- Ethylene-Propylene-Diene-Monomer (EPDM)
- Polychloroprene (CR)
- Acrylonitrile-Butadiene Copolymer (NBR, HNBR)
- Chlorosulfonated Polyethylene (CSM)
- Fluoroelastomer (FKM)
- Polyacrylate rubber (ACM)
- Epichlorohydrin rubber (ECO)
- Silicone rubber (VMQ)
-
Different synthetic rubbers work well in applications that involve oil and gasoline, animal and vegetable oils, some alcohols, and hydrocarbon solvents.
All rubber is either natural rubber or synthetic rubber, but unless you’re a rubber specialist, it might be hard to tell the difference.
Have a unique rubber challenge? Need professional insight?
Vulcanization and Rubber Compounding
In 1839, Charles Goodyear discovered the process of rubber vulcanization. This process—which improved properties like heat resistance, hardness, elasticity, and tensile strength of natural rubber—paved the way for further expansion of rubber manufacturing and production.
Early vulcanization treated natural rubber with sulfur. Since the early 1800s, various other methods of vulcanization have been developed.
Rubber compounding, by comparison, is the process of adding even more nuanced mixing processes and complex ingredients to a natural or synthetic rubber base. Rubber compounds are used to further enhance various qualities.
Rubber compounds often include:
- A base elastomer
- Fillers (natural or synthetic minerals, activators, and colors)
- Plasticizers (oils, liquids, esters, ethers)
- Antioxidants
- Cross-linking agents and accelerators
- Polymer resins
- Processing agents like soaps and waxes
- And other components for bonding, heat resistance, and more
Some rubber compounds are harder and more resilient than others. Some compounds offer higher heat resistance, and others excel at vibration dampening.
Every rubber compound recipe consists of different components. Each component has a very specific function, and each is added to the mix at a different stage of processing for desired effect.
AirBoss Rubber Compounds Outperform the Competition
AirBoss is a world leader in custom rubber compounding. As such, our R&D specialists look for new ways to improve existing compounds to create exciting new ones that meet emerging industry demands.
We didn’t become rubber experts overnight. It’s our decades of experience and a willingness to try things that other rubber manufacturers can’t or won’t that set us apart from the competition.