There are few milestones in rubber manufacturing history as influential as vulcanization, but others have also revolutionized rubber at the time of their discovery.
Silicone rubber is one such milestone that changed rubber manufacturing forever. It may get lost amidst other synthetic rubber innovations, but silicone rubber is a staple throughout rubber manufacturing. What makes silicone rubber special? And why is it a rubber of choice for so many industries? Read on to find out.

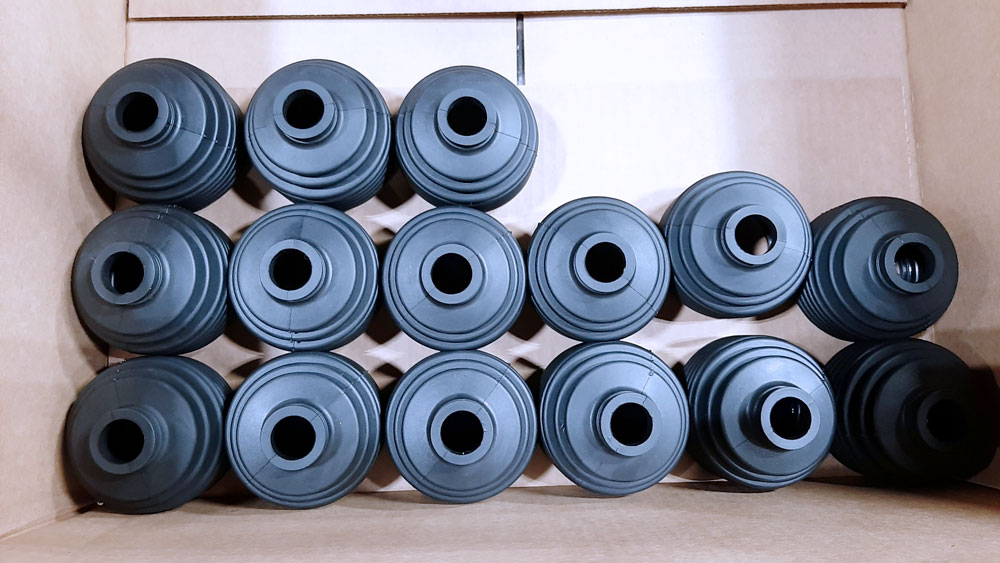
What is Silicone Rubber?
Silicone rubber, at its most basic chemical level, is known as a polymer. Polymers are chemical compounds formed from long repeating chains of molecules, and while they occur naturally (like proteins, starches, and DNA) they’re also created synthetically by material scientists.
Silicone—not to be confused with the chemical element silicon—is used in silicone oil, silicone resin, silicone grease and caulk, and silicone rubber. Silicone rubbers are one- and two-part polymers created from basic elements like silicon, oxygen, hydrogen, and a number of fillers and additives.
Uncured silicone rubbers are a gel-like adhesive liquid. This uncured rubber must be processed to be turned into a solid, and the process used determines the “type” of silicone rubber.
Silicone rubber processing can include:
- Platinum-based curing
- Condensation curing
- Peroxide curing
- Co-polymerization
- Acceleration of the curing process through catalyzation
- And more
Many of the silicone rubber processing methods pioneered by mid-1900s rubber innovators like Frederic Kipping, Dow Chemical Company, and General Electric Company are still used today, and rubber scientists like those at AirBoss continue to push the limits of what can be done with silicone rubbers.
It’s this kind of experimentation that led to silicone rubber’s creation in the first place, and it’s why silicone rubbers continue to influence rubber manufacturing.
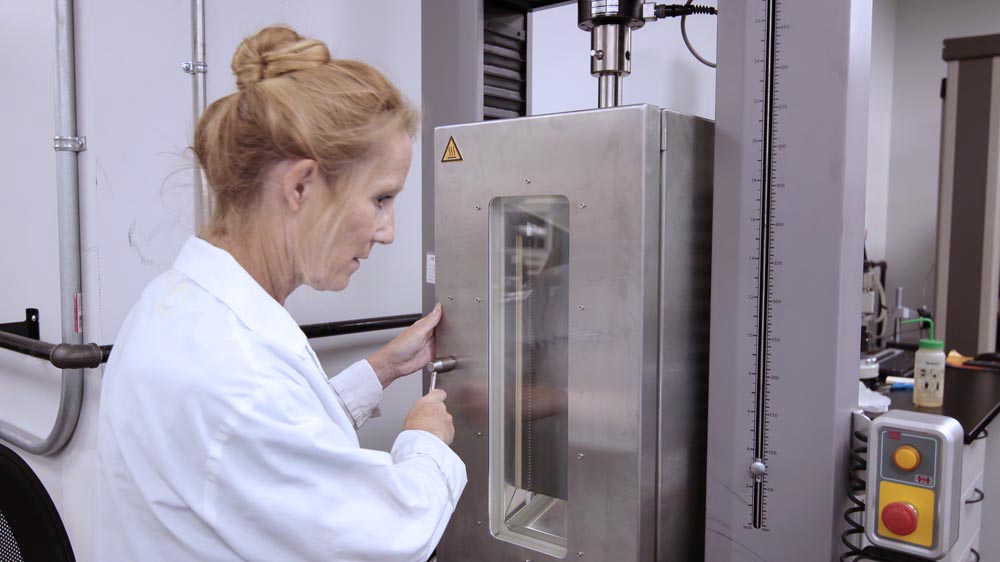
How Silicone Rubber Influenced Rubber Manufacturing
Throughout history, silicone and silicone rubber applications have influenced consumer product creation and commercial material application.
Silicone rubber is used in the adhesive used in Post-It notes, the silicone sole of astronaut Neil Armstrong’s boot that made the first footprint on the moon, and the first widely-used contact lenses, which used a silicone called hydrogel. It’s safe to say that silicone has made an impact.
The sought-after properties of silicone are what makes silicone rubbers so versatile, and these properties continue to drive material scientists to new application avenues.
How Modern Manufacturers Use Silicone Rubbers
Silicone rubber is only one tool in a rubber manufacturer’s toolbox. As such, experienced rubber manufacturers like AirBoss know how to use silicone rubbers to solve application challenges for automotive, aerospace, defense, healthcare, and other clients and industries.
We do so through a few different manufacturing processes:
- Extrusion: Silicone rubber can be extruded (pushed through) various dies to create cross-sectioned tubes, strips, and cords.
- Injection molding: Silicone rubber can be injection molded into simple or complex shapes.
- Assembly: Silicone rubber components are often assembled with other components and materials to create more complex parts and products.
- 3D printing: Modern silicone rubber compounds can be used as a base material for 3D printing applications.
Have a unique rubber challenge? Need professional insight?
Properties that Make Silicone Rubbers So Special
Silicone rubbers may be only one of many elastomers, polymers, and synthetic materials that modern rubber manufacturers utilize today, but they’re some of the most common, depending on the application.
Silicone rubbers are widely used in commercial and consumer products for their:
- Sealant capabilities: Silicone rubbers are used to create things like O-rings and gaskets to seal out chemicals and oils.
- Chemical resistances: Silicone rubbers have a low chemical reactivity; they don’t break down easily or quickly when exposed to some chemicals.
- Temperature tolerances: Silicone rubbers retain their properties over a wide range of temperatures, which makes them ideal for high-heat applications.
- Water-repellent properties: Silicone rubbers repel water exceptionally well and, as a result, are used in rubber hosing and gaskets to create strong seals.
- Electrical insulation: Some silicone rubbers can be processed in a way that makes them ideal for electrical insulation.
AirBoss material scientists believe traditional silicone rubber applications are still important, but it’s also our job to improve processes, refine compound formulas, and experiment with rubber solutions in ways that exceed customer expectations. It’s why our partners keep coming back when they have exciting ideas but need practical expertise.
AirBoss Continues to Innovate with Silicone Rubbers
Companies that make waves in industries like electric vehicles (EVs), military and defense, and healthcare innovation demand partners who understand their material needs. They don’t want status quo as much as they want progress, which is why many come to AirBoss to push the limits of what rubber can do.
EV makers come to AirBoss when they need rubber parts that reduce vibration. Defense contractors contact AirBoss when they need rubber-infused mobility systems that can stand up to extreme conditions. And healthcare organizations rely on AirBoss when they need local rubber solutions to combat unprecedented health emergencies.
None of this would be possible without silicone rubbers. They are one of our foundational pillars around which we create, prototype, and innovate.
Want to work with the silicone rubber experts? Contact AirBoss Rubber Solutions today!