Vulcanization — the process of hardening and improving rubber — changed the way rubber was created, processed, and used way back in the 1830s. Today, vulcanization continues to play a critical role in how modern rubber manufacturers like AirBoss work with the material.
Chances are you’ve heard the term vulcanization floating around the rubber world and for good reason. Without vulcanization, the rubber (and the companies that rely on it) would be very different.
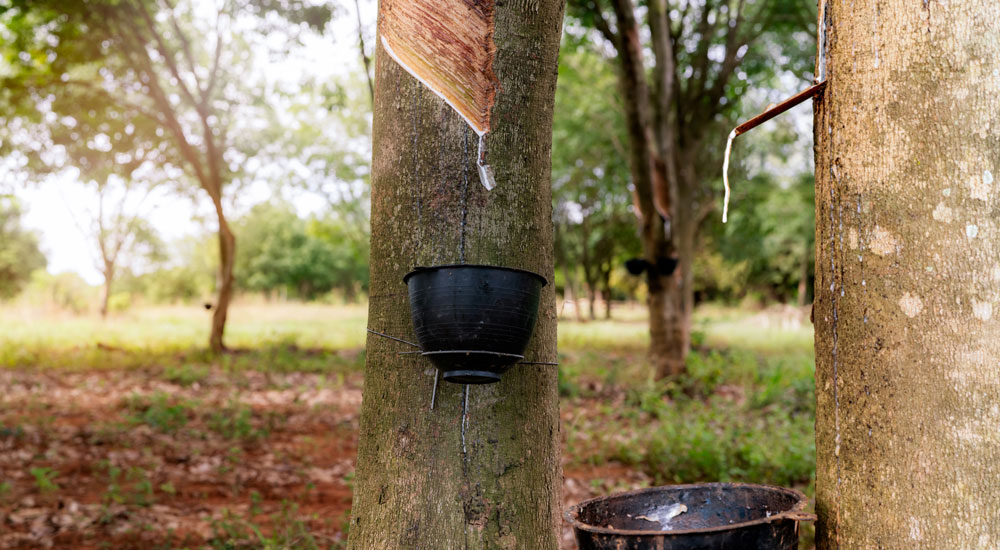
Rubber Before Vulcanization
Rubber before vulcanization was mostly natural latex rubber and was limited in its application. The earliest form of natural rubber, as well as its modern equivalent, is gathered by tapping into rubber trees to harvest the latex sap. This sap is then processed in various ways to yield a usable natural rubber.
Early commercial use of natural rubber was primarily for its water-resistant properties, its ability to stretch and retain its shape to some extent, and for being able to hold air when formed into a tube-like that of a bicycle or automobile tire.
Unfortunately, natural rubber, as resilient and miraculous as it was in the early 19th century, also had its drawbacks, which is what prompted vulcanization and the creation of synthetic rubbers.
Problems with early natural rubber for commercial use included:
- Low heat resistance
- Low chemical/oil/grease resistance
- Restrictive tolerance thresholds
Natural rubber products melted in high heat, deteriorated when exposed to chemicals and oils, and broke or cracked when stressed. So practical applications were limited, and it spurred rubber pioneers like Charles Goodyear to seek ways to optimize rubber for commercial use.
Have a unique rubber challenge? Need professional insight?
Charles Goodyear Discovered the Vulcanization Process
Rubber that melts, deteriorates, and breaks isn’t ideal for practical use, so the material was used sparingly in the early 19th century. What’s more, rubber products were often returned to the manufacturer because of decomposition and stickiness. In response, Charles Goodyear and other engineers and chemists around the world in the early 1830s tried to maximize rubber’s natural properties.
For years, Goodyear tried to find a combination of rubber and other additives that would improve durability, but his repeated attempts failed. His process heated up natural rubber to soften it for easier mixing. This sometimes produced a harder rubber, but this was because he cooked the rubber rather than added any other chemicals or other additives.
History says Goodyear went a little rubber crazy over the next few years as he, in a makeshift laboratory, combined rubber with various chemicals to see what happened. It almost ruined him, both financially and as a family man, because he was forced to sell almost everything he and his family owned (including his children’s books) to continue his work.
Charles Slack wrote in his Goodyear biography, Noble Obsession, that the rubber fanatic spared selling a set of China teacups only because the cups could also be used to mix rubber.
By accident, one day in 1839, one of Goodyear’s concoctions, a rubber/sulfur mix, fell onto a hot pan on the stove. The mixture stabilized and got harder rather than melt and boil as Goodyear expected. So, he turned up the temperature, and to his surprise, the mixture got even harder.
And that, believe it or not, was how Charles Goodyear discovered vulcanization. There’s more to the story, of course, and Goodyear wasn’t alone in his discovery, but that’s basically how it happened.
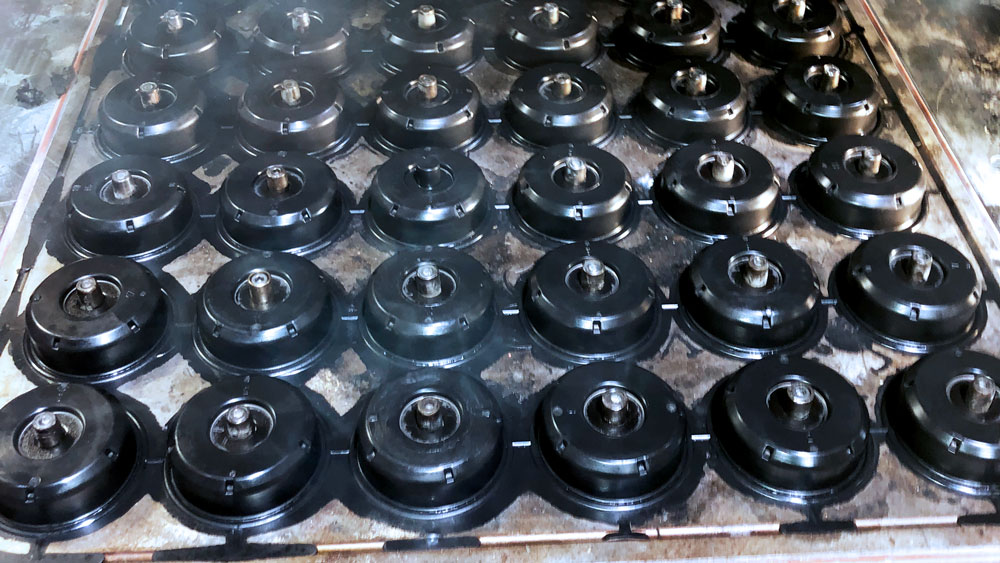
Vulcanization Today
It’s surprising that the process of vulcanization hasn’t changed much since the 1830s. Manufacturers like AirBoss still use sulfur as an additive when they create custom synthetic rubber compounds, and we’ve gotten even better at it over time.
Today, vulcanization has evolved to incorporate all kinds of different additives, chemicals, and extra ingredients. For example, neoprene and CR rubber are vulcanized with metal oxides instead of sulfur, and silicone rubbers are vulcanized using a reactive mixture of polymers, peroxide or platinum catalyst systems, and mineral fillers.
Regardless of the method, vulcanization today is still used to improve the properties of natural rubber.
Benefits of vulcanization include:
- Water repellency
- Oxidation and abrasion resistance
- Organic solvent (acids, chemicals) resistance
- Increased density
- Improved tensile strength
- Good electrical insulator
- And more
Today, vulcanized rubber is used in practically everything that uses rubber components. Rubber hoses, belts, tires, bushings, dampers, insulators, etcetera are made possible thanks to vulcanization.