Next-Generation Solutions at a Fraction of the Cost
If you’ve followed our adventures at AirBoss of America Corp., you know we’re always pushing the boundaries in custom rubber compounding design and formulation.
Challenges in our industry never stop evolving, after all – and neither do we! And on that score, we’ve been cooking up some new things behind the scenes that we think will shake things up a little.
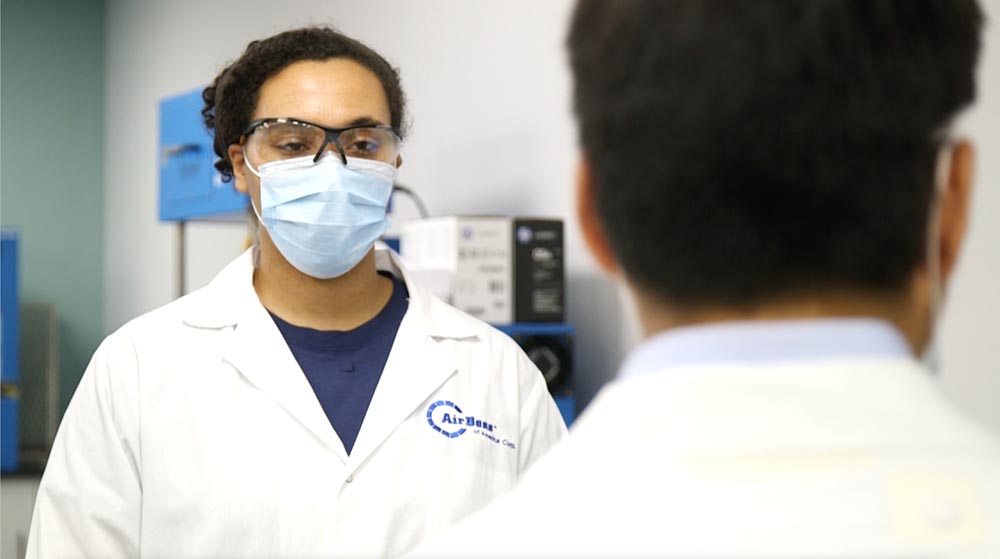
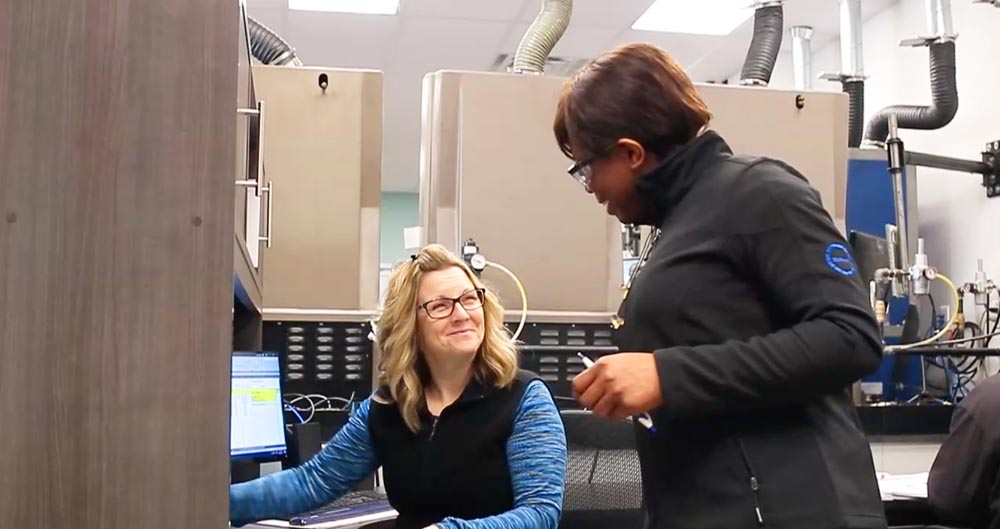
A New Recipe for EPDM – High Heat
Over the past couple years, we’ve been working on a new formulation for EPDM, or ethylene propylene diene monomer, that’s more cost-effective for our clients, easier to produce, and resilient at high temperatures. Here’s how we did it.
The time: June 2018.
The location: AirBoss of America HQ.
The goal: Develop a new EPDM formulation to replace silicone at temperatures ranging from 300-350ºF
Simple enough on the surface, but our engineers had their work cut out for them. Prior to 2020, over 100 unique formulations had been trialed to accomplish this goal, using a variety of EPDM grades, fillers, oils, antioxidants, co-agents, and peroxides – all without much success.
(The closest candidate only passed 70hrs at 350ºF, but even this formulation was too scorchy to be processable.)
Those familiar with AirBoss know that our exploratory chemists view this process not as a setback, but as an exciting challenge to overcome. We believe any obstacle can be tackled with the right planning and know-how, and fortunately for us, that know-how came in the form of a new in-house chemist who was able to help crack this code.
Next Generation EPDM at a Fraction of the Cost
Backed by our exceptional engineering team, AirBoss gained a new perspective on selection of diene types, co-agents, accelerators, and peroxides that allowed us to reformulate the compound.
Additionally, we made a few in-house modifications to our screen testing process and Design of Experiment (DoE) methods. There was a lot to take on, but the effort paid off.
We were able to develop an optimal HeatBoss formulation that passed 350ºF for 672 hours! Nearly 10x longer than our previous attempts. This new formulation can even meet the requirements of SAEJ200, grade E.
(To date, this is the only known EPDM compound that takes a spot in automotive muffler hanger application, which has been traditionally dominated by silicone.)
And best of all? Our new HeatBoss EPDM compound comes at only 50-60% of the cost of silicone and bears a similar level of processability. Though the formula is still new, we’ve received positive reviews from customers who have evaluated the compound for themselves. We’re optimistic that other clients will enjoy the same benefits when the time comes.
Next Steps: HeatBoss Goes Live
Our new EPDM compound is set to offer manufacturing advantages not previously seen in rubber compounding, and we’re eager to let others know!
In terms of next steps, we filed a patent provision in March 2021. There’s also a research paper on the subject submitted for publication in Rubber World journal, and another paper submitted to the Rubber in Automotive Conference.
Lastly, we’ve successfully registered and finalized the HeatBoss trademark! As our products continue to develop, we’re hoping the HeatBoss brand will come to represent the same values and commitment to quality as the rest of the AirBoss family. We’re off to a strong start – and the sky’s the limit!