Rubber manufacturing has come a long way since the substance was first discovered.
No one can be one hundred percent certain, but the earliest known appearance of what we consider rubber today dates back nearly three millennia. Urban rubber legend says that some time in the 1600s B.C.E., native peoples of Central and South America collected natural rubber, rolled it into balls, and played games with it. As time went on, the substance’s many other useful properties came to light.
Rubber was used in the construction of early tools, as a water repellent when applied to clothing, and was (allegedly) given the name “rubber” in the 1770s when Joseph Priestly noticed the gummy substance could rub out pencil marks.
By 2021, global demand for natural rubber exceeded fourteen million metric tons, so it’s safe to say that the manufacture and distribution of rubber is big business. As a result, custom rubber compounders like AirBoss continue to produce high-quality natural and synthetic rubber products, compounds, and innovations.
But how does the whole process work? Where does rubber come from, and how is it manufactured on a global scale?
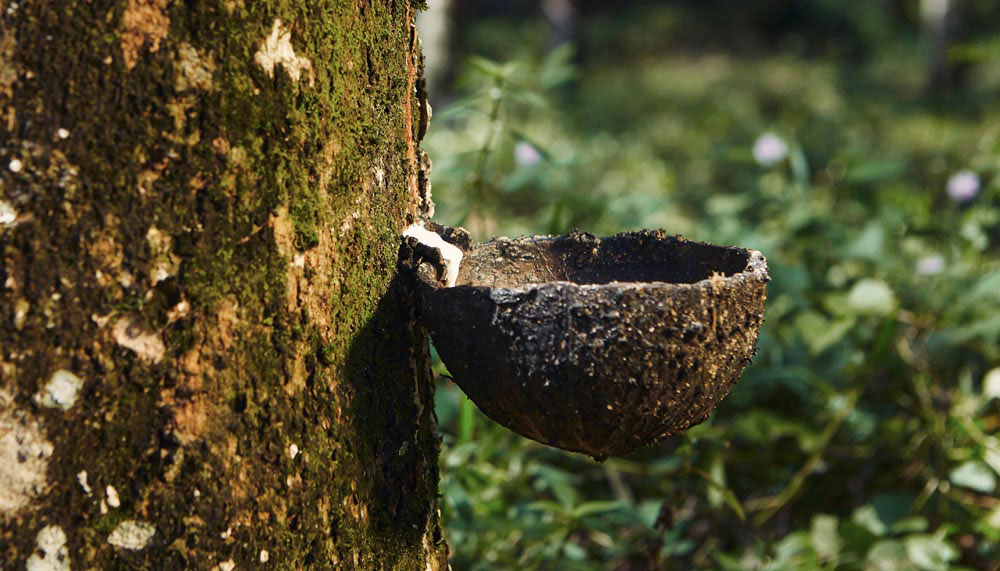
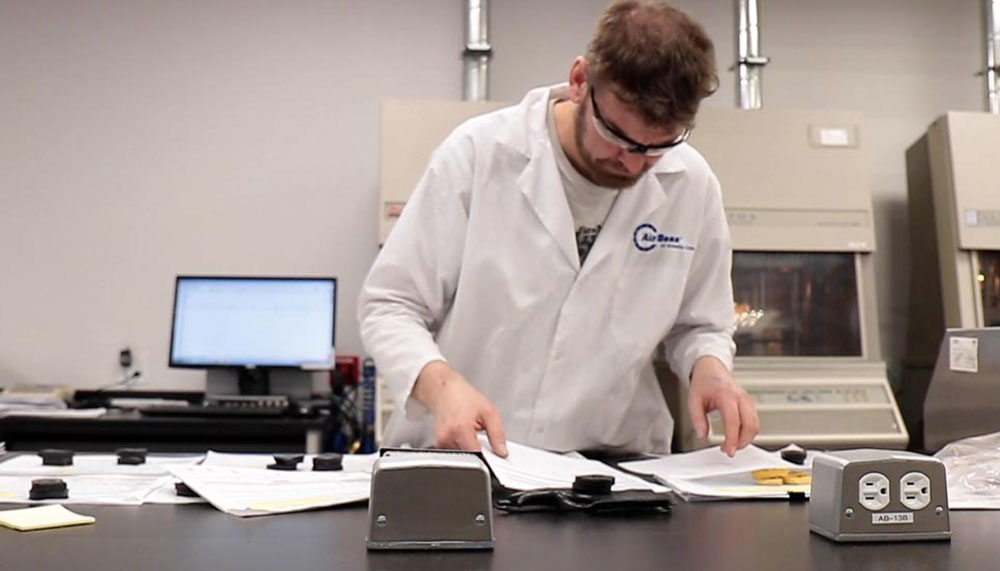
Rubber Tree Latex and Natural Rubber
The purest, most natural form of rubber is made from the milky white latex sap harvested from rubber trees. Rubber trees grow in hot, moist climates, and most of the world’s natural rubber-producing trees are found in Africa, Asia, and Central and South America.
To harvest the sap, which is called “rubber tapping,” a groove is cut into the tree. Then the bark is peeled back and removed. This allows the latex sap to run down the tree where it is collected.
Rubber tapping is a sustainable practice since the tree is not cut down, and organizations like the Global Platform for Sustainable Natural Rubber aim to keep rubber manufacturing as natural as possible.
Latex sap, once collected, is made ready for processing. This pre-processing:
- Adds ammonia to keep the latex from solidifying
- Adds acid(s) to coagulate and extract the rubber
- Passes the sap through rollers to remove excess water
- Air dries the resulting substance
Upon completion, the once-liquid natural latex sap is ready for its final processes and manufacturing. Both natural and synthetic rubbers require extra processing before they’re ready for practical applications, but we’ll get to that in a bit.
Have a unique rubber challenge? Need professional insight?
The Invention of Synthetic Rubber
Historians will tell you that the invention of synthetic rubber was a result of a limited natural supply and enthusiastic chemists sometime around World War II. However, almost one hundred years before that war, scientists played with polymers and created elastomers.
Researchers like Michael Faraday (1829) and Greville Williams (1860) broke down the chemical makeup and created their own liquid synthetic “isoprene” replicants.
Efforts to replicate natural rubber continued as chemical analyses and laboratory processes improved. By the early 1920s, countries like the Soviet Union, Germany, and the United States produced tens of thousands of tons of synthetic elastomers and used them to manufacture tires and other rubber products.
Household tire names like Firestone, Bridgestone, B. F. Goodrich, and Goodyear revolutionized synthetic rubber production and manufacturing during the mid-1900s, and as a result, it became more available and just as reliable as its natural counterpart.
According to Statista, the global synthetic rubber market in 2021 was estimated to be more than $19 billion.
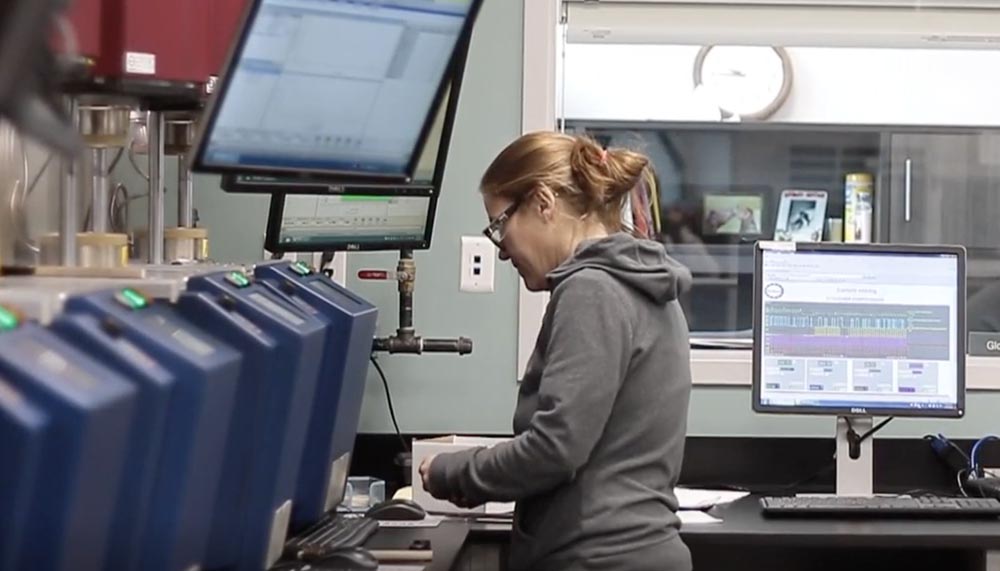
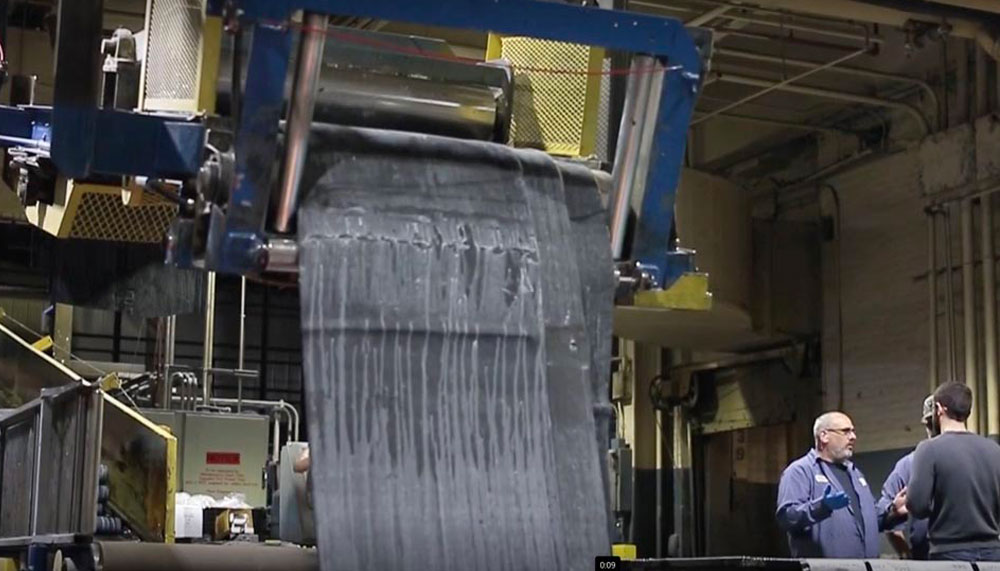
The Finishing Touches of Rubber Manufacturing
Both natural and synthetic rubbers need to undergo some finishing touches before they’re ready for the market. Without these final processes, most rubber would be unusable for practical applications.
Un-processed rubbers:
- Are brittle when cold
- Get sticky when hot
- Can be unstable
- Are not very durable
- Don’t retain their shape
- And more
That’s why rubber — both natural and synthetic — undergoes additional processing. Often, chemicals and fillers are added to increase durability, strength, and longevity. Depending on the application, different polymers are added to a mixture, and chemical combinations are fine-tuned to create custom rubber compounds designed to improve or refine specific properties.
Hot rubber solutions are then cooled before they’re shaped, pulled, rolled, squeezed, or molded into their desired shape.
Last but certainly not least, many rubber compounds are vulcanized—treated with a curative—to further reinforce the compound and make it more durable.
Rubber, Rubber Everywhere
That’s about as Rubber 101 as it gets to help you understand rubber’s processes and manufacturing—from tree to tire. Today, rubber products and compounds are used around the world in myriad ways for countless applications.
Companies like AirBoss continue to refine their processes to bring unique qualities to custom compounds and create high-quality rubber products. And it all starts with some natural latex sap and a handful of combined polymers.